Lean es una palabra inglesa que se puede traducir como magro o esbelto. Aplicado a un sistema productivo significa ágil, flexible, es decir, la capacidad de adaptarse a las necesidades del cliente. El concepto Lean también se aplica a otros campos, donde ha recibido los nombres de “Lean Production”, “Lean Management” o “Lean Logistics”.
El Sistema Lean Manufacturing tiene su origen en el sistema de producción desarrollado por Taiichi Ohno en los años 50 -durante su trayectoria profesional en la compañía automovilística Toyota-, conocido como Toyota Production System (TPS).
En la década de los 80, empresas japonesas, americanas y europeas ya conocían este sistema de producción y comenzaban a aplicarlo. Pero no fue hasta el año 1990, cuando J. P. Womack y D. T. Jones, documentaron el Sistema de producción Toyota en su libro “The Machine that changed the world”, al que titularon “Lean Manufacturing”.
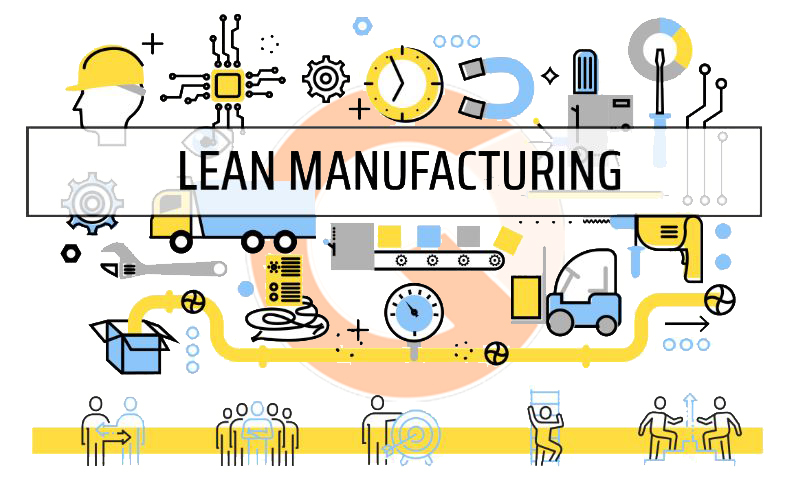
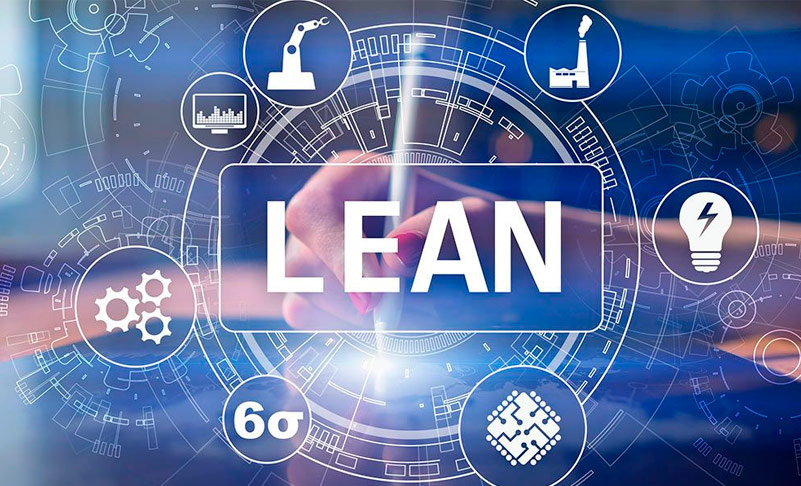
Estos mismos autores han publicado el libro “Lean Thinking”, donde además de exponer los principios básicos de un Sistema de producción Lean Manufacturing, se explica la evolución que ha sufrido este nuevo pensamiento Lean y las nuevas herramientas dirigidas a aplicar con éxito esta metodología.
¿Por qué aplicar lean manufacturing?
Los sistemas de producción Lean son útiles para todas las empresas, todas desarrollan operaciones para dar valor al cliente.
Empresas productivas y de servicios ven en los sistemas de producción ágiles la oportunidad para mejorar sus operaciones.
Ágil significa mejorar reduciendo dinero, personas, equipos grandes, inventario y espacio, con dos objetivos: sin despilfarro y reduciendo la variabilidad (Seis Sigma).
¿Qué implica lean manufacturing?
La implantación de un Sistema de Producción Lean implica:
- Asumir tres revoluciones conceptuales: redescubrir el papel fundamental del producto, crear un sistema de producción pulsante con el mercado, y la mejora en un brevísimo plazo de tiempo.
- Una nueva filosofía en la organización: enfoque centrado en la acción y perseguir la perfección a través de la reducción del MUDA (despilfarro).
- Una nueva organización: una nueva estructura basada en las familias de productos y un nuevo papel del personal operativo.
¿Cómo se hace lean manufacturing?
6 SIGMAECUADOR se basa en el enfoque de Toyota y lo completa con la visión más avanzada:
– Diagnóstico. Análisis del flujo de materiales y de información. A través de la realización del Value Stream Mapping (VSM) se diagnostica el estado del proceso productivo actual y se propone un flujo de valor futuro. En este proceso se resuelven problemas cómo:
- Cómo se relaciona la demanda del cliente con la capacidad de producción (takt time)
- Cómo y dónde crear flujo continuo
- Cómo trasladar la demanda del cliente al proceso productivo
- Cómo y dónde nivelar productos
- Cómo llevar a cabo todo el proceso
– Implantación a través de la combinación de semanas Gemba y proyectos clásicos de mejora combinados con una adecuada gestión del cambio. El equipo mixto cliente-consultor desarrolla el proyecto y consigue los resultados.
– Seguimiento de resultados y continuidad del proyecto. A partir del seguimiento de 5 indicadores clave (calidad, eficiencia, velocidad, entrega y valor) es el cliente quien decide la bondad del proyecto y la continuidad de la experiencia.
¿Qué beneficios obtengo?
La aplicación sistemática de enfoques de producción Lean permite a diferentes tipos de compañías obtener resultados como:
– Aumento de la productividad: 300 a 400% si se fabrica por lotes y 100% si se fabrica en flujo
– Rotación de inventario: -95% si se fabrica por lotes y -80% si se fabrica en flujo
– Defectos: -95% si se fabrica por lotes, -75% en caso de fabricación en flujo
– Plazo de fabricación: -95% en caso de fabricación por lotes y -75% si se fabrica en flujo
La sostenibilidad de estos resultados en el tiempo lleva asociada la creación de una estructura (Kaizen Promotion Office).
¿Qué ofrece 6 sigma ecuador a su organización?
Diagnóstico Lean:
– Realización de Mapas del Flujo de Valor (VSM)
– Revisión de todas las áreas funcionales implicadas en producción
– En una o en todas las fábricas de la corporación
– Identificación de oportunidades de mejora
– Selección de proyectos
– Cuantificación de resultados
Puesta en marcha del modelo:
– Formación a todos los niveles
– Lanzamiento de proyectos operativos
– Despliegue de indicadores
– Creación de la estructura organizativa
– Acompañamiento en proyectos
– Obtención de los resultados
Realización de eventos Gemba Kaizen
Integración con otras técnicas:
– Seis Sigma
– TPM (Total Productive Maintenance)
– PMC (Proyectos de Mejora Continua)
– ISO 9000
Formación y sensibilización:
– Formación a directivos y mandos (TPS + herramientas)
– Jornadas de sensibilización
– Formación a operarios
– Cursos “in company”, a medida, personalizados